End tabbing of composite test specimens – Practical tips
In a previous article, I covered the importance of alignment when testing composite specimens. For that reason, it is vitally important that steps are taken to ensure correct alignment of the test coupons from the start of the tabbing process.
Alignment
Aligning a unidirectional composite can be easily achieved by using the ‘chocolate bar’ snap test, where you can easily snap the laminate along the length of the fibre. With a non-unidirectional sample however, you must physically trace the fibre direction using an indelible marker prior to machining. Ensure that the laminate is machined with a square edge along the fibre direction, when machining down to the required tabbing geometry.
Pre-treatment
In order to get a good quality bond between the end tab and the test specimen, there is a need to first ensure there is a suitable bonding surface. There are two ways to ensure this. The most common way is to mechanically abrade the bonding surface of both the end tab material and the test material. The goal is to both remove any surface contamination, such as mould release agents, greases or oils and to key the surface, in order to aid mechanical bonding.
This can be done by either grit blasting, or by hand sanding. It is important that during this operation, only the outer resin layer of the laminate is removed, without causing any damage to the underlying fibres. Once abraded, make sure that the bonding surface is suitably cleaned and solvent dried before proceeding to applying the adhesive. A useful tip In order to check if the surface is suitably abraded is to carry out a water break test. This involves pouring water on the surface of the abraded material. If it is not suitably abraded, then the water will gather in a number of small puddles on the surface, whereas a well abraded sample will lead to the water gathering as a solid film on the surface of the end tab. An example of this can be seen below, where the water has been dosed with red food colouring in order to more clearly show the water agglomeration on the surface of the tab material.
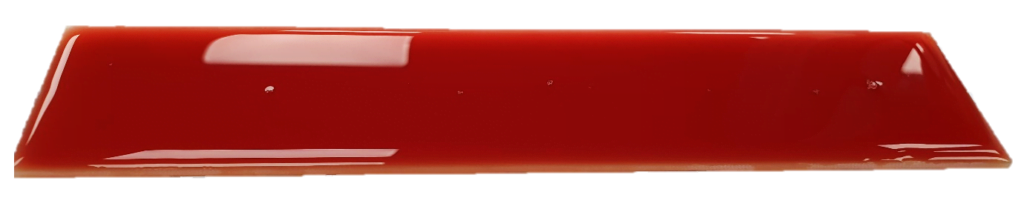
Figure 1 – Water break test carried out on non-abraded sample on the top showing coloured water patches and an abraded sample below, showing a solid film of coloured water
An alternative solution is to chemically etch to bonding surfaces. This comes with the benefit of reducing the amount of fibreglass dust that becomes airborne from the pre-treatment process. An example of such a chemical etch can be found from Oxford Advanced Surfaces, with their ONTO adhesion promotion range.
Bonding the end tab
Adhesive selection is just as important as tab material selection. The adhesive must be able to transmit the applied load into the test specimen via shear and must withstand the compressive force applied by the grips. The ability to control bond line thickness is also desirable, as this can allow for the design of the tab region to be manipulated in such a way as to further reduce the stress concentrations.
Either a film or a paste adhesive can be used to bond the end tabs to the surface of the laminate. The choice of adhesive really depends on the application. For example, paste adhesives tend to have a smaller window of operating temperatures, however their application is simpler.
Film adhesives require a combination of temperature and pressure in order to cure, whereas paste adhesives will cure readily under ambient conditions. The benefits of film adhesives are the ease with which you can control the bond line thickness and the larger operating window of test temperatures. However, care must be taken when using a film adhesive, to ensure that the cure temperature of the adhesive does not exceed the post cure temperature of the test material or the end tab material.
As far as paste adhesives are concerned, commercially available two part epoxy resin systems have been found to be suitable for bonding end tabs. Whichever adhesive is used, it should be tough, with a greater strain to failure than the test material and have a shear strength in excess of 30MPa. It is important while using a paste adhesive, to ensure that the adhesive is applied to both the end tab and the composite panel during tabbing. Steps should also be made to control the bond line thickness. This can be done through the use of wire spacers, fishing wire, or using a layer of vacuum infusion distribution mesh.
How thick should the bond line be? Well it depends on the nature of the end tab. For tapered end tabs, the bond line thickness has no significant effect on tab termination stress concentrations, however with un-tapered specimens, such as for compression testing, a bond line thickness of 1.3mm is recommended.
Tab alignment
Alignment of the tab on to the material surface can have an impact on the alignment of the specimen within the grips. A well aligned tab can aid this, however, oversized or poorly aligned tabs can lead to the sample becoming misaligned within the grips of the machine. Furthermore, some compression standards specify the maximum misalignment between the tabs, from one side of the specimen to the other. Therefore, it is important to take steps to ensure good quality alignment during the bonding process. In order to achieve this alignment, it is recommended to use a fixture for the tabbing process. An example of which is commercially available from the Wyoming Test Fixtures website. The fixture is aluminium, which allows for suitable heat transfer through the fixture should an elevated temperature be required for the adhesive.
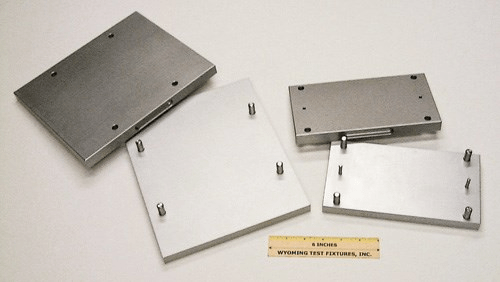
Figure 2 – End tabbing fixture from Wyoming Test Fixtures
The fixture’s base plate is fitted with pins, against which the strips of tabbing material can be aligned, to ensure a consistent specimen gauge length. After applying the adhesive, place the test material on top of the tabbing material, between the alignment pins. Repeat the process for the other side and then finally, attach the top plate. After this point, carry out the cure schedule as required.
References
- Adams, D.F. Tabbing composite test specimens: The how. Composites World 2011
- Adams D.O. & Adams, D.F. DOT/FAA/AR-02/106 Tabbing Guide for Composite Test Specimens, October 2002
- . Hodgkinson, J.M. Mechanical testing of advanced fibre composites, CRC Press, 2000